How Having an A&P Benefitted Me Part 2
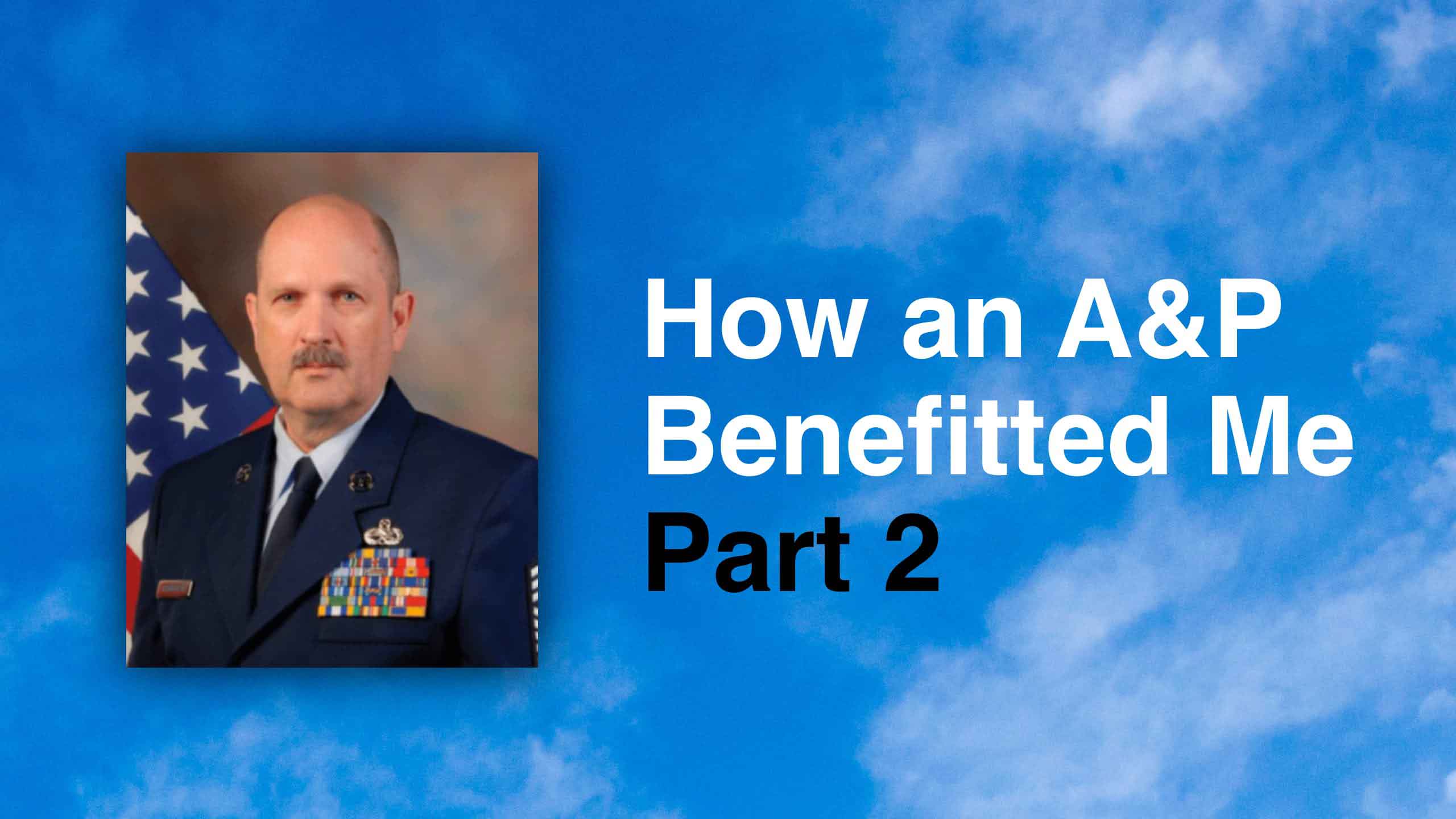
I signed up for A&P school not quite knowing what I was getting myself into. For one it was a privately run school and if I remember correctly the tuition was around $8,000 and that was 1977 dollars. I’m pretty sure we didn’t get the loan paid off until the early part of this century. But it was a top-rated school even though the timing was bad. Spoiler alert – when I graduated there were very few jobs available for new mechanics. One was working for a really bad freight dogger flying out of Detroit and the other was a contract for Bell Helicopter working in Iran right before the revolution and the fall of the Shah of Iran. But I’m jumping ahead of the story.
One of the things they recommended for school was a scientific calculator. Spoiler alert! I’m old. Most smartphones today come with both a basic and a scientific calculator, and if they don’t then you just download a free app. Not the case in early 1977. I purchased the cheapest one I could find and it was made by Texas Instruments and probably cost me every bit of $100. In today’s dollars that’s about $430 and minimum wage was $2.30 and hour. Some guys bought Hewlett Packard programmable calculators and I was just a little jealous because those things were $300 and up. My first car (a 57 Chevy) cost $300 and it was a graduation present from my parents.
In any case, I showed up for class and the first block of instruction was the general subjects which included FAR’s, Weight & Balance, Math, and Physics, etc. Our class started with like 38 students and by the end of that first four weeks we lost 10 people who just never came back and another 10 dropped out over the next 18 months. Two of them I know dropped out because they didn’t want a job where they couldn’t smoke pot. One was an acid head and knew he couldn’t pass the Writtens. Yeah, life in the 70’s. Lol!
About four months in I realized that I was going to need a job since my savings were running out. I happened to have just started the Electrical Block and I saw a job in the newspaper for an arcade attendant. Yes, the only way back then to find a job was in the employment section of the newspaper called the Want Ads. Remember, no PC’s and no internet in 1977. I told you that I was old. Now I happened to love arcades and thought it was a perfect job so I called the number and got an interview. I mean, how hard could it be to make change once in a while and make sure that kids weren’t vandalizing the machines? The manager asked about my background and asked if I knew anything about mechanical things. I told him that I was in A&P school to be an aircraft mechanic and was currently (pun intended) taking the electrical section. He told me that was great because if I could fix aircraft then I would be able to fix the arcade games when they broke down.
What?!?!? Fix the machines?? I didn’t say it out loud but the ad just said attendant not arcade technician. I really wasn’t a mechanic at this point and was just learning the basics of car maintenance from my dad. And I had just started the electrical block. But I really wanted the job and the hours were perfect for school so I just nodded in agreement and he hired me. So my A&P got me a job even before I had my tickets. This was to be the first of many strange twists in my life and career. How little I knew then about where it would all lead me.
The first few weeks were great fun and the job was in a mall so I got off work early enough that I could get some sleep before going to class in the mornings. Then one evening fate caught up with me. One of the pinball machines broke down. Now these were old school electromechanical machines and not electronic at all. I tried turning it on and off a few times but that didn’t work so I then unplugged it and plugged it back in again. Nope. I tried kicking it and shaking it and even putting more coins in it. Nope. All of my advanced troubleshooting was to no avail and so I had to open the machine up. The manager hadn’t even shown me how to do that so I had to figure it out on my own. I finally got the playfield lifted up and stared in shock at what greeted my eyes. It looked like a very complicated robot had thrown up in this thing. Thousands of wires, hundreds of open leaf blade relays, and dozens of coil solenoids. Truthfully I panicked. Falling back on my A&P training I decided that I needed to look at the wiring diagram. I located it and opened it up. I was aghast as this thing kept unfolding. It was about three feet long!
For what seemed like an eternity I stared at the diagram and the guts of this inoperable beast that was laughing at me. What to do? Do I just leave it broken and fess up to the manager, or do I take a stab at this thing? Thankfully I chose the latter and it was a slow night. My first action was to reach down into this thing and try to move some of the relays by hand to see what happened. After all, the diagram showed 24 and 6 VDC in the machine so it should be safe right? Wrong! There were areas of line voltage and the machine let me know that right away. First lesson learned. Read the whole diagram (or task) before you begin and make sure that you understand what you are dealing with.
So I jumped back to the information I had learned in the Electrical Block at A&P school and started reviewing the wiring diagram. Honestly, I was still in a bit of a panic but eventually I saw an item listed as “Start Relay”. I thought that might have something to do with it and I looked in the machine and eventually found a relay with the same label. Making sure this time not to touch any bare metal or wires I reached down inside and moved the contacts. Amazingly the machine started! I was so proud of myself and closed up the machine and tried to start a game. But nothing happened. So much for my troubleshooting skills. As it turns out it the start relay was the problem, I just hadn’t fixed it. After a little more analysis and panic I eventually figured out that a set of contacts needed to be cleaned and adjusted and the game was up and running.
When I came in the next afternoon the manager asked me about the repair since he had read about it in the log. Of course, the 18-year-old me didn’t mention the fear and panic and instead just covered the details rather nonchalantly. He was duly impressed (or so I thought) and within a few weeks he gave me a raise and a few months later I was made assistant manager. Things went well until through a series of unfortunate events the arcade was robbed overnight and everyone lost their jobs. Sadly I had previously informed Corporate that is wasn’t a good idea to keep large sums of money locked in a plywood cabinet in an office with access via a drop ceiling. Apparently it was easier to fire me rather than deal with the corporate security manager that I had informed.
In any case this led me to a new job working for a place called Malibu Grand Prix. They ran multiple locations where you could drive scaled down Formula cars and also had a large arcade. They had just opened a new location in Denver and needed an Arcade Technician. They also maintained the cars in their own garage and because of being in A&P school I got the job and eventually moved into the role of assistant manager. If I remember correctly, I kept this job through A&P school.
Then there was a follow-on job with a huge entertainment complex in Denver called Celebrity Sports. 200 bowling lanes, a restaurant, three bars, Olympic size swimming pool and five arcades.
Somewhere in this timeframe, right after graduating from school I got my first A&P job. Remember that jobs for A&P’s were scarce in the late 70’s but I saw an ad for a mechanic at the Arapaho County Airport which is now I believe the Centennial Airport. I went out to interview and they guy just told me to meet him out on the ramp at a gold colored Chevy station wagon. I just figured that he was busy with fixing something on a plane and that he didn’t have time to do the interview in his office or at the FBO. His name was Rich and the interview was a little weird but he hired me on the spot. Then he told me he was assigning me to work with another mechanic and told me to hop in the station wagon. He had me fill out an application and a W-2 sitting there in his car. Again, just a little out of the norm. Then we drove off and I thought I was going to get to see the hangar. Wrong! Instead we drove across the ramp and pulled up to yet another station wagon packed with equipment and tools.
There he introduced me to Ike and told me that I would be working with him and he promptly sped off in a haze of oil smoke. But within a few hours I discovered a few things. The first revelation was that there was no FBO or hangar. This company was a guy who literally repaired aircraft out of the back end of a bunch of station wagons. If you needed jacks they were in the gold station wagon. If you needed the scales for a weight and balance they were in the red station wagon. We had air compressors but no generators or inverters so when the tanks ran out we had to go plug them into an outlet somewhere. Nearly everything was done out on the ramp and this was Fall/Winter in Denver. It really was the true definition of line maintenance.
My second revelation revolved around Ike. As it turned out, Ike was a cool guy, very funny, and I liked working for him. He was a Korean War vet and worked on helicopters and every time it got cold he would tell the story about how the collectives on the helicopters would freeze up in the cold in Korea and how they went about thawing them out. The story always ended up that they urinated on them. Remember that this is Fall/Winter in Colorado so you can guess how many times I heard this story. I couldn’t figure out why he kept telling the story over and over again until I realized that he was an alcoholic. Every time something didn’t go right, or when things went really well, he pulled out a hip flask and took a shot.
Even though it was a crazy operation I definitely learned a lot about GA aircraft. I also learned that the owner was just a bit of a whack job. One event that showcased his “issues” was the replacement of a windshield on a Rockwell aircraft. This one happened to look a lot like a 172 and he gave us the new windshield to install. We removed the old one but the new one just plain didn’t fit up on top. It sat too high by about 2 inches. We called him over and he said we just didn’t know what we were doing. He climbed up on top of the wing and started pushing down on the Plexiglas. It still wasn’t budging so he put his knee into it and after a few good pushes the plastic broke. He totally trashed this brand-new windshield. He went ballistic and started throwing tools and stomping on the windshield in a rage. I decided then that this was not going to be long-term employment with this guy. The problem with the windshield was that he just assumed that a 172 one would fit since they looked the same and the 172 one was a little cheaper. Another few lessons learned for me. Firstly, just because something looks the same doesn’t mean that it is. So always use the IPC/IPB. Secondly, forcing something to fit usually doesn’t end well.
And I learned one last lesson working there. Very late one afternoon I had to remove and reinstall an alternator that was mounted on the rear gearbox of an Aeronca I think it was. During the process I dropped one of the mounting nuts. I thought I heard it hit the ramp and looked everywhere but couldn’t find it. There really wasn’t anyplace in the firewall area it could have landed since it was all open to the ground. I gave up and installed a replacement nut, did an ops check and went home, even though that missing nut was bugging me. That night I couldn’t sleep because of that stupid piece of hardware and I knew the plane was going to fly first thing in the morning. So I got up and got dressed and went all the way back out to the airport in the pitch dark. I opened up the cowl and removed the alternator and as I tilted it out the missing nut fell out of it. It had been lodged inside the cooling fan area but hadn’t done any damage. But as I looked at the design I saw that it could have moved to a position where it would have damaged the alternator and possibly resulted in the loss of the aircraft and pilot.
The lesson learned was, always listen to your conscience or your inner-voice. If something doesn’t seem right then it probably isn’t. Don’t ignore it and think that things will be fine. Once I got back home I slept soundly with a clear conscience. For the few hours I had left before I had to get up and go to work. Lol!
Coming up in the next installment. Arcades seemed to be going nowhere (which looking back they were starting their death spiral) and my wife of only five months suggested I join the Air Force. She was an Air Force brat and thought it would be a good way for me to get to work on airplanes. Spoiler alert. I join and having my A&P helps yet again in unforeseen ways.